6 Week Series: Maintaining Internal Controls
Week 1: Capacity Planning
As manufacturers, we
often face tight delivery expectations and spacial constraints within our
facilities. This poses the absolute need for strict capacity planning and
attention to fluctuating resources, such a raw material and workforce
availability. At Bowman Tool we involve all relevant department managers in the
process of capacity planning. From warehousing to purchasing strategies BTM is
always seeking the most efficient and cost effective course of action.
Maintaining an
accurate view of building and equipment capacity allows us to throttle our
business activities appropriately. When done properly, capacity planning allows
manufacturers to reduce unnecessary overtime, improve delivery performance, and
relieves warehousing congestion. When customer demand increases, so does the
need for Internal Control.
Week 2: Effective Processes
Manufacturing is all
about effective processes and procedures. Streamlining each piece of the
manufacturing pipeline is what truly manages the flow of work from the first
contact with the Customer all the way through to Production and
Shipping of finished goods. At Bowman Tool we have mapped each step of the
manufacturing process from the inside out. This allows us to assign roles,
divide labor, catch discrepancies, and continuously improve without constantly “putting
out fires” in areas that were unmonitored. Like any business, these processes
are ever-evolving to the standards and requirements of the Customer.
The obvious advantage to maintaining Effective Proccess Management is the basic clarity of expectations and requirements for each stage. However, a closer look shows that Effective Processes also allow us to:
- Identify goals and objectives
- Identify critical success factors
- Understand key performance drivers
- Identify strengths and weaknesses in procedures
- Benchmark against past performance
Bowman Tool also greatly benefits from an intense Quality Management System in accordance with ISO 9001:2008. ISO not only allows our company to standardize our quality practices but also shows our Customers that we take continuous improvement and meeting the requirements of our customers very seriously.
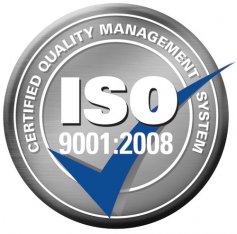
Week 3: Sunrise Meeting
One of the most
important pieces of our ongoing improvement efforts begins with daily team
meetings with the BTM leaders. First there is a sunrise meeting among the
department heads where the most pressing issues are discussed and plans are
made. Then Operator meetings on the shop floor are led by our Team Leads in
which supplier and material issues, scrap and efficiency rates, new product
introduction, quality control, and preventative maintenance are discussed with
Operators to ensure transparency and understanding throughout the facility.
BTM stresses
communication at all levels of the manufacturing process. We strive to provide
the highest level of Customer Service by developing a lasting working
relationship founded on trust and the reliability of open communication. BTM
management stresses the importance of this team-led approach as it brings the
different departments together in the shared objective of meeting and exceeding
Customer expectations.
Week 4: ERP
Like many manufacturing
companies, Bowman Tool utilizes a Enterprise Resource Planning (ERP) system
to plan the requirements throughout the facility. Financial Management, Supply Chain, Production, Scheduling, Product Data, Service, Human Capital, Sales, and Customer Relationship Management are all areas we are able to monitor through the ERP. With this we are able to
confidently make daily operation decisions as well as monitor long-term
planning and utilization of resources. By making strategic choices based on the
data collected and analyzed in the ERP system we are able to reduce downtime, increase productivity, and continue to focus on our Customers.
Week 5: Continuous Improvement
We at BTM take
improvement very seriously. So seriously that it is a part of our Quality
Policy Statement:
“BTM Delivers Superior
Products to Customers by Adhering to Standards of Quality, Integrity, and
Excellence with an emphasis on
Continuous Process Improvement.”
This statement is
visible throughout or facility and is upheld by all of our employees. Our
management team meets weekly in a Quality Improvement Initiative meeting to
discuss ideas and designate resources to improvement areas. Our Quality
Initiative focuses on the Continuous Improvement of efficiencies, internal
processes and procedures, product quality, employee development, and general
work flow for our operators. From these meetings we are able to allocate
attention to the matters at hand and determine the best course of Change
Management.
Week 6: Change Management
It is rare that any form
continuous improvement works perfectly the first time around. Many ideas take
ongoing finessing and molding to form the desired result. This is essentially why
Change Management is extremely important. When an idea for change is proposed
in our Quality Initiative meeting, it is then worked with interdepartmentally
until a solution is found. The solution is then brought back to the table and
reexamined for further opportunities for improvement. Many revisions may be
made before the change has met the needs and satisfaction of the team. We
involve Quality, Production, Shipping/Receiving, Engineering, and HR to evolve
these changes into something that serves the company as a whole and where all
aspects of the situation are evaluated. This is one of the many reasons why
Bowman Tool excels in production manufacturing.
Follow Us...
Bowman Tool & Machining
is dedicated to keeping you up to date on industry news and current events
related to Manufacturing. We invite you to follow us on the following
platforms:

|